c-Com Software Platform
Discover our innovative solutions
Collaborative Tool and Life Cycle Management
With the background of the leading metal cutting tool expert, c-Com was established to improve collaborative processes within the tooling industry. First applications focused on sharing data between a tool supplier and its customer, for example when exchanging tools for refurbishment, working together on optimizing tools and exchanging information such as drawings and issues. Naturally all data evolved around tools and their digital twins. Today we differentiate ourselves with collaborative processes, the ability to share data securely, bring various forms of data together and put them in a tooling context.
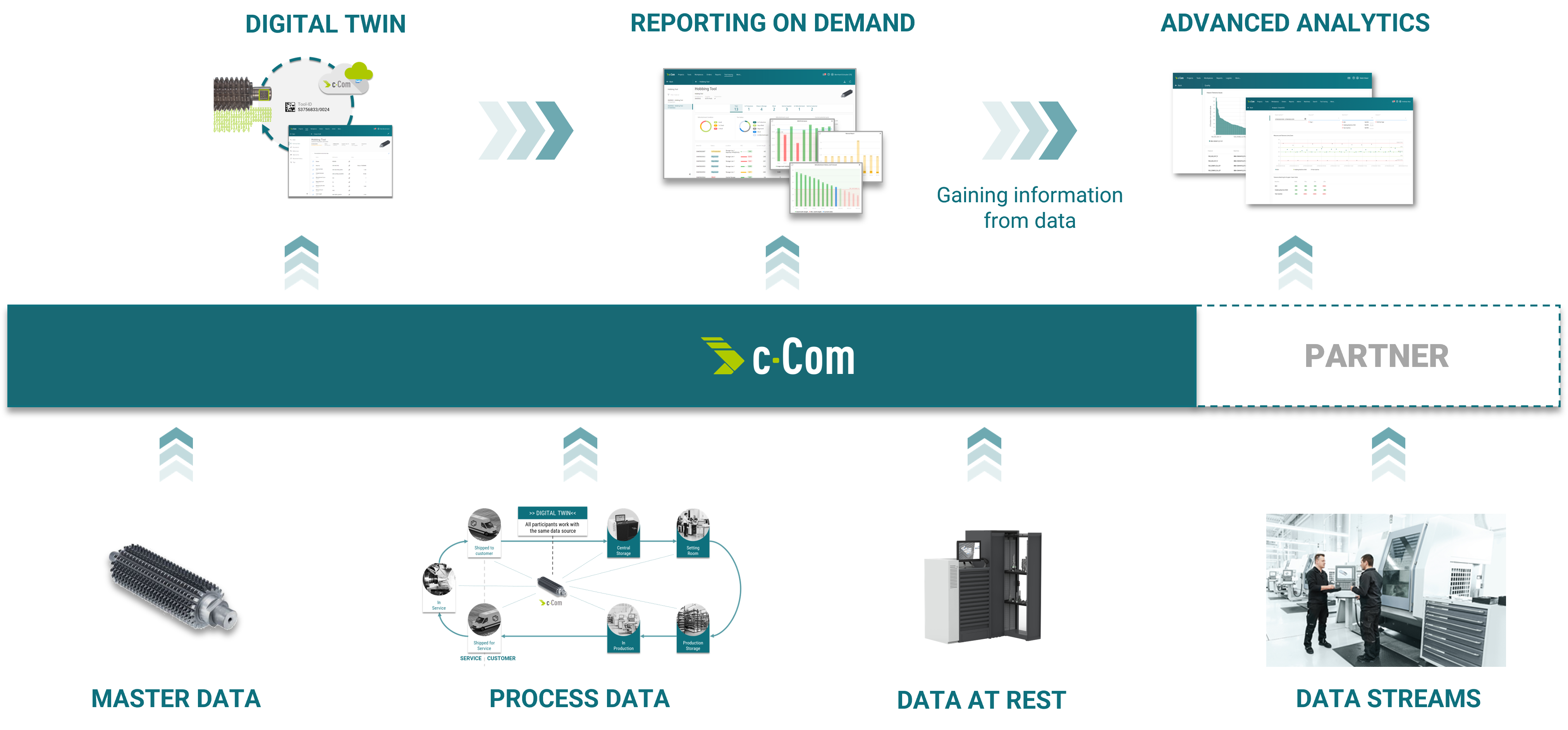
Often our customers are confronted with the question whether to make or buy a tool management software solution. While an internal solution has the advantage of a tight integration into the IT landscape and close proximity to the user, spending valuable software development and project resources on assistive processes (tooling is often considered a C-part) must withstand the critical evaluation of decision makers. c-Com’s modular software comprises of domain knowledge, customizable processes, regular updates and proven customer success.
Software Platform
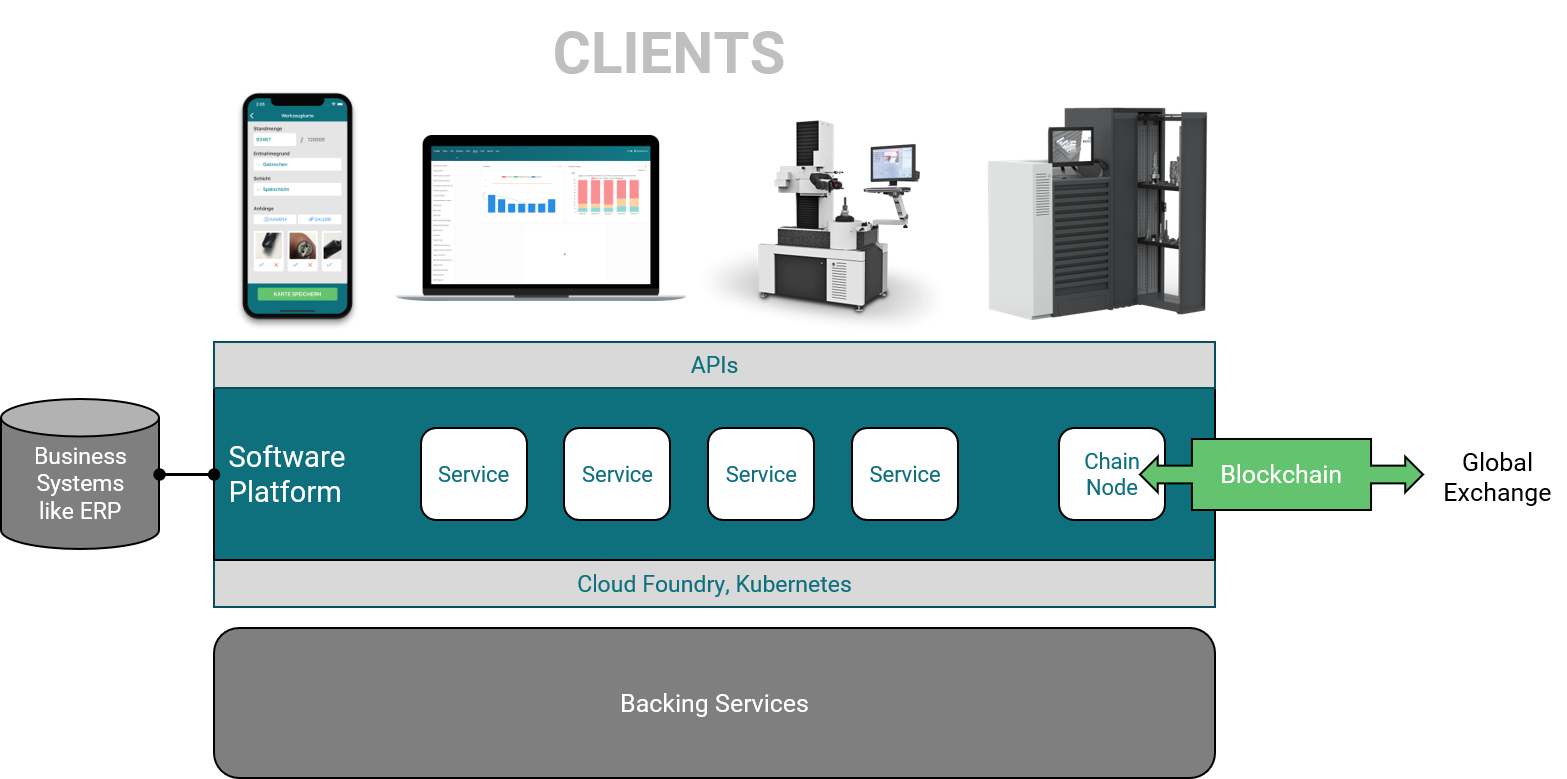
Built on a modern technology stack, c-Com’s service architecture allows to run its services on various infrastructures like a Cloud Foundry, Kubernetes Cluster or virtual machines. We recommend to use standard software for backing services such as PostgreSQL. Client connectivity is always abstracted through APIs, allowing for backward compatibility, extensibility, customization and adaptations.
Security & Privacy
We offer multiple data center locations through different cloud providers. For example in Frankfurt/Germany, London/United Kingdom and Shanghai/China.
Master and process data is stored in a database within the data center operating the application services. Personal data (e.g. username, password, e-mail-addresses) are stored outside either in a customer system or depending on the region in separately governed systems. Documents, prices and delivery times are typically stored within the premises of suppliers with only short caching times within the c-Com platform.
Depending on the c-Com version, region and environment this can be different parties, for example:
c-Com customers have access to their own data. Within public cloud offerings your c-Com account representitive typically has access as well as technical administrators. c-Com’s Private Cloud Edition has different accessibility.
c-Com’s software platform has multiple levels of authorization. Typically a customer administrator receives access to the entire organization. Within this he can create organizational units (groups), roles and users to control who is allowed to access which parts and data in the system.
In the Public Cloud Edition this feature is deactivated. In the Private Cloud Edition, this is possible.
Public Cloud Edition: Modern Web Browser such as Microsoft Edge or Google Chrome
Private Cloud Edition: Application Server(s) or Platform (e.g. Kubernetes or Cloud Foundry) and at least one PostgreSQL or HANA Database Service.
c-Com stores and processes personal information such as names and e-mail-addresses for the purpose of identifiction, authentication and notification. This confidential information is kept in a separate service, e.g. SAP Identity and Authentication Service (IAS) or keycloak. This separation ensures that non-personal information cannot be linked directly and that different maintenance processes and access privileges can be applied.
Tool Manager App
With the native Tool Manager app, tool managers and sales representatives can draft reports about tests or tool issues quickly and easily and share them in real time with the concerned people, for example the product manager or the development engineer. Pictures, videos and other different files can be attached and transferred for a comprehensive analysis and report. Trouble shooting and optimizations become in this way extremely fast and efficient.
Tool Assistant App
With the Tool Assistant App c-Com supports your mobile applications such as scanning a tool in production to know its state and remaining usage, creating delivery papers for refurbishment and pairing components to an assembly, withdrawing or storing tools in managed storage locations, recording tool life and change reason of a tool and much more. Available on Windows, iOS/iPad OS/Mac OS and Android you have great lexibility to deploy the application to different hardware. Depending on the platform, you have additional options like including advanced scaning software to save on scanner hardware, read information from a RFID chip and customized print-outs.
Integration & Standards
Typically the c-Com software is integrated with the customers OT and IT environment. In the overview below common integration scenarios are depicted. However, this list is not enhaustive so if you find an interface technology that you require, please contact us directly.
System to integrate | Format | Interface Technology |
ERP, e.g. SAP ECC or S4/HANA, Microsoft Navision | OpenTrans, XML IDoc, XML, CSV, JSON | Web Service, Network File Transfer*, proprietary |
CNC Machine, Machining Center | JSON, XML | Stream Integration via Broker, e.g. MQTT, Kafka |
Dispensing System, e.g. Kardex, Hänel, MAPAL UNIBASE, KROMI KTC | JSON, XML, CSV | Web Service, Network File Transfer*, proprietary |
Presetting Device, e.g. Kelch, MAPAL UNISET | JSON, XML, CSV | proprietary |
Part and Quality databases | Tables, CSV, JSON, XML | Web Service, JDBC*, ODBC* |
Tooling Systems | JSON, XML | Web Service |
* Only available in the c-Com Private Cloud Edition
System to integrate: ERP, e.g. SAP ECC or S4/HANA, Microsoft Navision
Format: OpenTrans, XML IDoc, XML, CSV, JSON
System to integrate: CNC Machine, Machining Center
Format: JSON, XML
System to integrate: Dispensing System, e.g. Kardex, Hänel, MAPAL UNIBASE, KROMI KTC
Format: JSON, XML, CSV
Interface Technology: proprietary
System to integrate: Presetting Device, e.g. Kelch, MAPAL UNISET
Format: proprietary
System to integrate: Part and Quality databases
Format: Tables, CSV, JSON, XML
Interface Technology: Web Service, JDBC*, ODBC*
System to integrate: Tooling Systems
Format: JSON, XML
Interface Technology: Web Service
* Only available in the c-Com Private Cloud Edition